|
 |
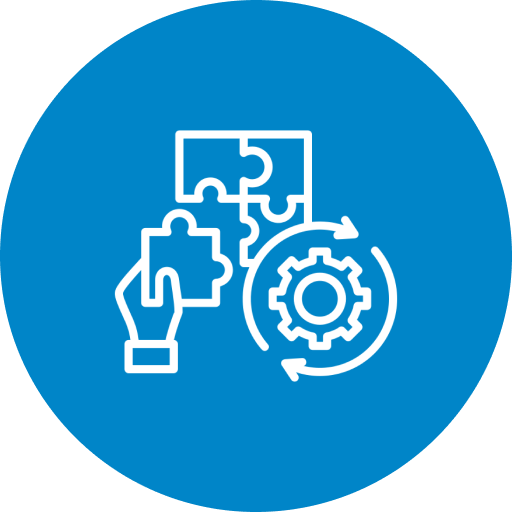 |
|
Total Engineering Solutions |
|
 |
We provide total engineering solutions to resolve root issues in problematic rotating equipment such as pumps, blowers, and compressors that, if left to progress, will lead to catastrophic failures. |
|
|
Causes of Issues |
 |
Most underperformance and failures (e.g. seal leaks) in rotating equipment are due to imbalance, misalignment, wear and looseness, leading to excessive vibrations that accelerate wear and lower power efficiency. |
|
|
|
|
 |
Our Solution Process |
 |
CFD Flow Simulation |
 |
Using computer-assisted Computational Fluid Design (CFD), our teams analyse and understand how interacting components in rotating systems behave. Based on the flow simulation, our team redesigns and modifies the equipment for improve efficiency, reliability and safety. |
|
|
Reinforcement |
 |
Certain spare parts for the rotating equipment may be outdated, expensive, or even obsolete. Replacing these parts might not offer a sustainable solution, as the problems could resurface over time. To provide a more permanent solution, we offer total redesign and reinforcement services to strengthen and fine-tune the equipment. |
|
|
|
 |
|
|
However, developing accurate blueprints for reversed engineered parts is a highly technical challenge that is prohibitively expensive if carried out manually. |
|
|
|
|
 |
|
 |
Our Solution Process |
 |
Computer-Assisted 3D Scanner Design |
 |
Using computer-assisted Computational Fluid Design (CFD), our teams analyse and understand how interacting components in rotating systems behave. Based on the flow simulation, our team redesigns and modifies the equipment for improve efficiency, reliability and safety. |
|
|
|
 |
|
 |
Our Solution Process |
 |
Detailed Analysis |
 |
To determine areas for improvement, rotating equipment and its components will be disassembled, cleaned, photographed, and inspected for a detailed analysis. |
|
|
Fabrication, Assembly & Testing |
 |
Once the changes are determined, components that need to be replaced are measured, modelled in CAD, and sent to a third party for fabrication. The component is then collected, reassembled, and tested for optimal function. |
|
|
|
 |
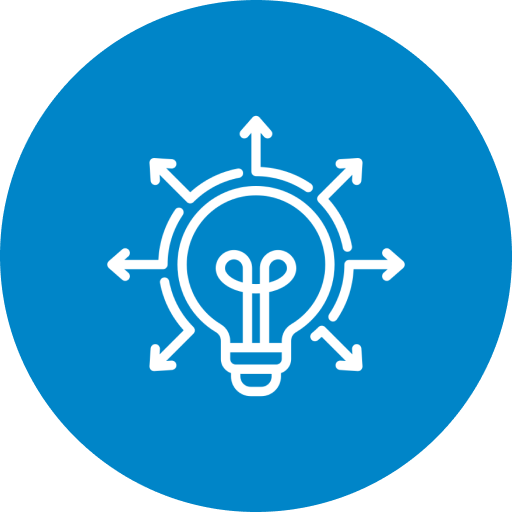 |
|
Refurbishment & Supply of Existing/New Mechanical Seal |
|
|
|
Replacing worn mechanical seals is a significant cost associated with operating high-performance rotating equipment, with damage often resulting from rotor misalignment, seal incompatibility, excessive heat, improper installation, and poor storage conditions. |
|
|
|
|
 |
|
 |
Our Solution Process |
 |
Lapping & Polishing |
 |
Using a combination of lapping and polishing, it is possible to smoothen the surfaces of mechanical seals to working order with the exact surface finish and flatness tolerances for optimal functionality. |
|
|
Leak Test, Elastomer Upgrade & Site Installation |
 |
A leak test is performed and the elastomer is upgraded or replaced as necessary before the fully refurbished component is installed on-site. |
|
|
|
 |
|
 |
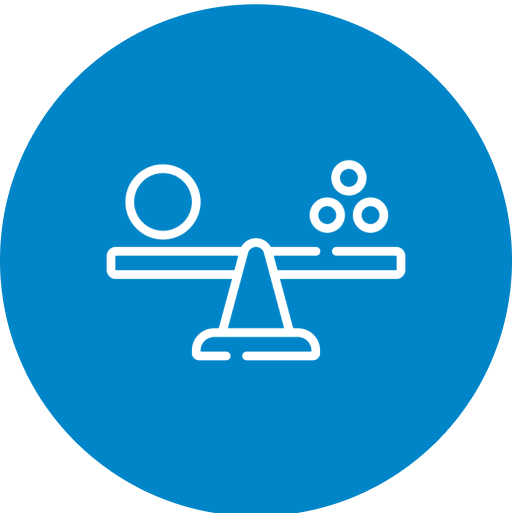 |
|
In Situ Vibration Analysis |
|
 |
For large equipment with vibration issues, we offer on-site services where our team conducts thorough analysis to identify any underlying problems, including potential structural issues. |
|
|
Depending on the condition of the equipment, we provide recalibration services to ensure optimal performance of the equipment, making necessary adjustments as required. |
|
|
|
|
 |
Our Solution Process |
 |
Operational Deflection Shape (ODS) Analysis |
 |
ODS combines dimensional and vibration data to create visual simulations of vibration patterns of a machine or structure - thus allowing for easy and accurate analysis to facilitate corrective actions. If issues are detected, a technical team will be sent on-site to assist with repairs. |
|
|
|
 |
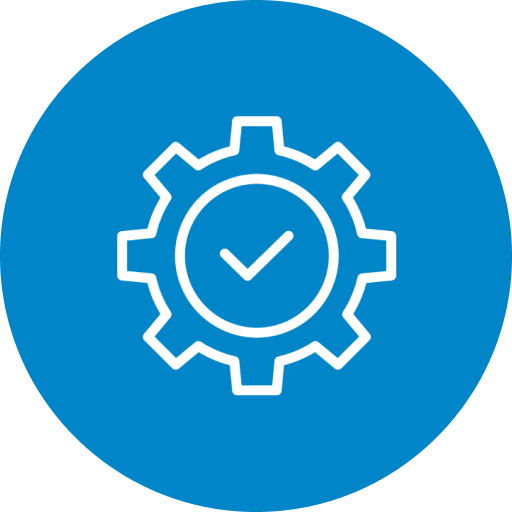 |
|
Balancing |
|
|
|
Over time, even well-built rotating equipment can undergo misalignment, cause imbalances, and produce vibrations that can damage their structure and components. |
|
|
|
|
 |
|
 |
Our Solution Process |
 |
In Situ Balancing |
 |
Our teams can carry out balancing while rotating equipment is operating and without dismantling and reassembly - thereby allowing for balancing issues to be resolved within days. |
|
|
Shop Balancing |
 |
For more complex balancing issues, rotating equipment will be transferred to our factory where balancing work can be carried out with heavy-duty equipment and specialised tools. |
|
|
|
 |
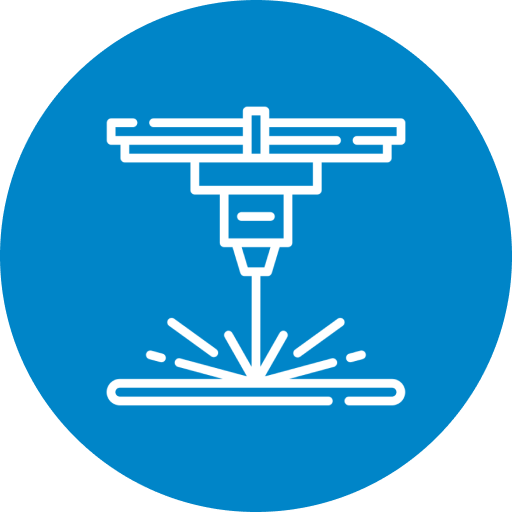 |
|
Laser Alignment |
|
|
|
When heavy rotating equipment operate at high speeds, any misalignment in the coupling shafts and other moving components can sufficiently damage bearings, seals, and couplings to result in catastrophic failure. |
|
|
|
|
 |
Our Solution Process |
 |
Laser Precision Alignment |
 |
Our teams utilise precise laser tools when realigning critical components (such as shaft couplings connections) back to correct operating tolerances. |
|
|
Graphical Interface & Computerised Alignment Report |
 |
In addition, our laser alignment solution technology is equipped with an intuitive graphical user interface that displays real-time vertical and horizontal alignment data to help minimise errors. |
|
|
|
 |